Welding is a critical process in the construction and manufacturing industries, and understanding Miller weld settings is essential for achieving high-quality welds. Whether you're a professional welder or a hobbyist, having the right knowledge about Miller weld settings can significantly improve your welding outcomes. This article will delve into the intricacies of Miller weld settings, providing you with the expertise and guidance necessary to achieve professional-grade results.
In today's competitive market, precision and efficiency are key. The right weld settings not only enhance the structural integrity of your projects but also save time and resources. By mastering Miller weld settings, you can ensure that your work meets industry standards and exceeds client expectations.
This comprehensive guide will cover everything you need to know about Miller weld settings, from the basics to advanced techniques. We'll also explore practical tips, expert advice, and industry best practices to help you refine your welding skills. Let's dive in!
Read also:Andrew Tate Kids A Comprehensive Insight Into Family Life And Legacy
Table of Contents
- Introduction to Miller Weld Settings
- Understanding Welding Parameters
- Types of Miller Welders
- Setting Up Miller Welding Equipment
- Advanced Miller Weld Settings
- Troubleshooting Common Issues
- Industry Best Practices
- Importance of Calibration
- Maintenance Tips for Miller Welders
- Conclusion and Next Steps
Introduction to Miller Weld Settings
Miller weld settings refer to the specific configurations and parameters used in Miller welding machines to achieve optimal welding performance. These settings include voltage, amperage, wire feed speed, and shielding gas flow rate. Understanding and correctly adjusting these settings are crucial for producing strong, clean, and visually appealing welds.
Miller Electric Manufacturing Company, a leading name in the welding industry, offers a wide range of welding machines designed for various applications. From small-scale projects to large industrial operations, Miller welders are known for their durability, precision, and reliability. By mastering the settings on these machines, you can unlock their full potential and enhance your welding capabilities.
Understanding Welding Parameters
Welding parameters are the key factors that determine the quality and strength of a weld. These parameters must be carefully adjusted based on the material being welded, the thickness of the material, and the welding process being used. Below, we'll explore two critical welding parameters: voltage and amperage.
Voltage
Voltage is the electrical potential difference between the welding electrode and the workpiece. It plays a vital role in determining the arc length and stability. For Miller weld settings, the recommended voltage range typically varies depending on the material and thickness. Generally, higher voltage results in a longer arc, which can lead to increased heat input and wider weld beads.
- For thin materials, lower voltage settings are preferred to avoid burn-through.
- For thicker materials, higher voltage settings can help penetrate deeper into the material.
Amperage
Amperage, or current, determines the amount of heat generated during the welding process. Proper amperage settings are essential for achieving the desired penetration and bead appearance. In Miller weld settings, amperage is often adjusted using the machine's control panel.
- Lower amperage is suitable for delicate or thin materials.
- Higher amperage is required for thicker materials or when deeper penetration is needed.
Types of Miller Welders
Miller offers a variety of welding machines designed for different applications and skill levels. Below are some of the most popular types of Miller welders:
Read also:Simone Biles News Pregnant The Latest Updates And Insights
- MIG Welders: Ideal for beginners and professionals alike, MIG welders are known for their ease of use and versatility.
- TIG Welders: Suitable for precision welding, TIG welders are commonly used in industries requiring high-quality welds.
- Stick Welders: These are rugged and reliable machines often used in outdoor and industrial settings.
- Multi-Process Welders: Combining multiple welding processes, these machines offer flexibility and adaptability for various projects.
Choosing the right type of Miller welder depends on your specific needs and the materials you'll be working with. Each type has its own set of Miller weld settings that must be carefully configured for optimal performance.
Setting Up Miller Welding Equipment
Proper setup of your Miller welding equipment is crucial for achieving consistent and high-quality welds. Here are some steps to follow when setting up your Miller welder:
- Inspect the machine and all components for damage or wear.
- Connect the power supply and ensure proper grounding.
- Select the appropriate welding process and adjust the Miller weld settings accordingly.
- Install the correct electrode or wire and set the wire feed speed.
- Adjust the shielding gas flow rate to prevent contamination of the weld pool.
By following these steps, you can ensure that your Miller welder is ready for use and will produce reliable results.
Advanced Miller Weld Settings
For experienced welders, understanding advanced Miller weld settings can elevate their skills to the next level. These settings include:
- Pulse Welding: This technique involves pulsing the current to control heat input and achieve precise welds.
- Hot Start: A feature that increases current at the start of the weld to improve arc striking.
- Anti-Stick: Prevents the electrode from sticking to the workpiece by reducing current when the arc is lost.
By experimenting with these advanced settings, you can refine your welding techniques and tackle more complex projects with confidence.
Troubleshooting Common Issues
Even with proper Miller weld settings, issues can arise during the welding process. Below are some common problems and their solutions:
- Porosity: Caused by contamination of the weld pool, this issue can be resolved by ensuring proper shielding gas flow and clean materials.
- Cracking: Often due to improper cooling or excessive heat input, this can be mitigated by adjusting voltage and amperage settings.
- Warping: Prevented by clamping the workpiece securely and using intermittent welding techniques.
By identifying and addressing these issues promptly, you can maintain the quality and integrity of your welds.
Industry Best Practices
Adhering to industry best practices is essential for ensuring safety and achieving high-quality welds. Some key practices include:
- Regularly inspecting and maintaining your welding equipment.
- Wearing appropriate personal protective equipment (PPE) at all times.
- Following manufacturer guidelines for Miller weld settings and equipment operation.
By incorporating these practices into your workflow, you can minimize risks and maximize efficiency.
Importance of Calibration
Calibrating your Miller welder ensures that all settings are accurate and consistent. Regular calibration helps prevent errors and ensures that your welds meet industry standards. To calibrate your Miller welder:
- Refer to the manufacturer's manual for specific calibration procedures.
- Use calibrated measuring tools to verify settings.
- Perform test welds to confirm the accuracy of the settings.
By keeping your Miller welder properly calibrated, you can maintain the quality and reliability of your welds.
Maintenance Tips for Miller Welders
Regular maintenance is essential for extending the lifespan of your Miller welder and ensuring consistent performance. Here are some tips for maintaining your Miller welder:
- Clean the machine and all components regularly to prevent dust and debris buildup.
- Inspect and replace worn or damaged parts as needed.
- Lubricate moving parts according to the manufacturer's recommendations.
By following these maintenance tips, you can keep your Miller welder in top condition and ready for any project.
Conclusion and Next Steps
In conclusion, mastering Miller weld settings is crucial for achieving professional-grade welds and enhancing your welding skills. By understanding the key parameters, configuring your equipment properly, and adhering to industry best practices, you can ensure that your welds meet the highest standards.
We encourage you to take the next step by experimenting with different Miller weld settings and techniques. Share your experiences and insights in the comments below, and don't forget to explore our other articles for more welding tips and advice. Together, let's elevate the art and science of welding!

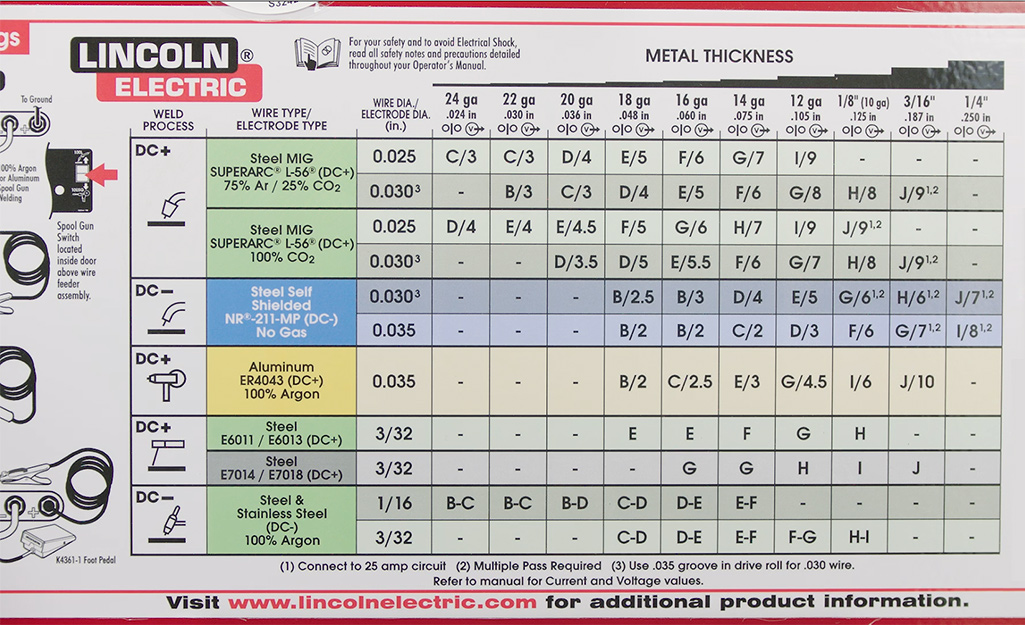